Ok, its been a while since I've been bitten by the humidity bug, but.... I have a build that I was getting ready to route the binding ledges in. Normally, I keep works in progress this far along indoors in a case. I got called away and managed to leave this in the garage for a couple of days just when we had our warmest days of the year and lo and behold shrinkage occured! About 4-5 inches on the lower bout to boot!
The split is right along the center seam with fibers and such still spanning the seam in places. Right now I am trying to ' re-humidify' in hopes of closing the gap, and then glue (CA?) but I am not hopeful of the outcome. Other than replacing the top, anybody have any thoughts/incantations/secret potions that may salvage it?
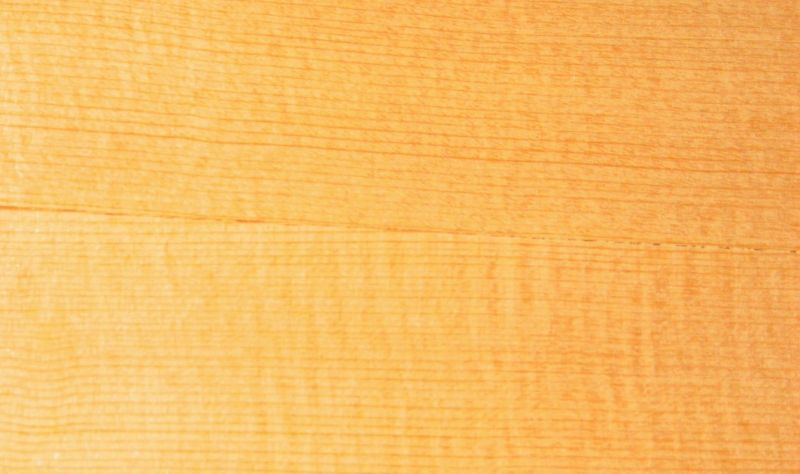
Did I mention there's beer in it if it works?