
Not being rigged up for a Weissenborn, and there's not much info available, it's been a little bit of a learning curve. So I'll try and document some of this build for others to follow. I'm no expert, so don't take any of this as Gospel. I reserve the right to change my mind about any of this as I go along.

Being too large for my radius dishes, I built a building board similar to one I saw on Christophe Grellier's web site. Along with a body mold and bending form.
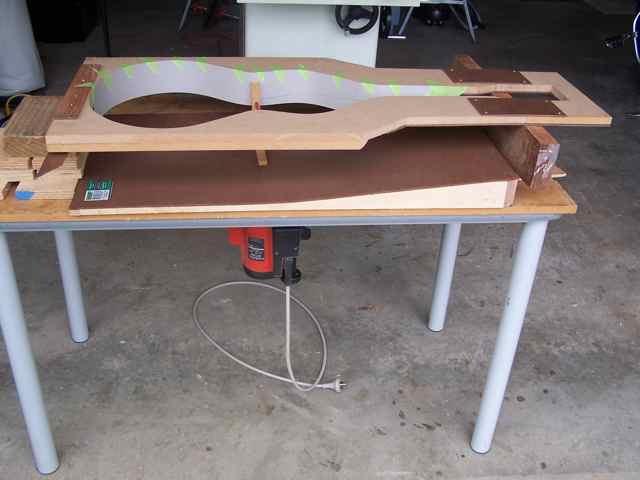
I have it propped up above the work board so that it's level in both directions, in order to make a template for profiling the sides.
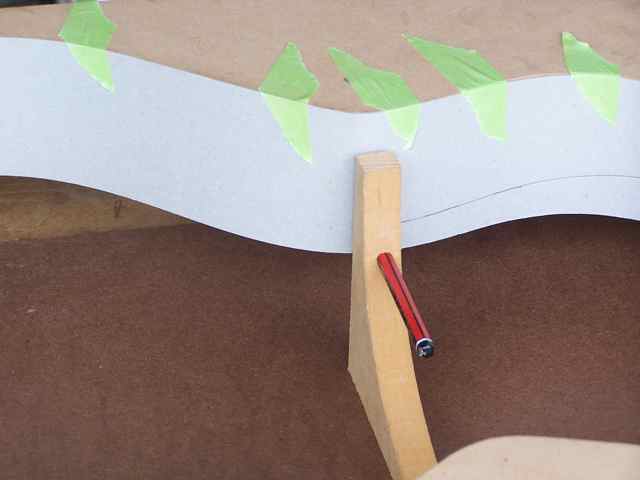
I attached a 3" wide piece of poster board to the mold. Note that the top edge is level with the top of the mold. Then I made a little jig to hold a pencil to trace the profile onto the poster board.
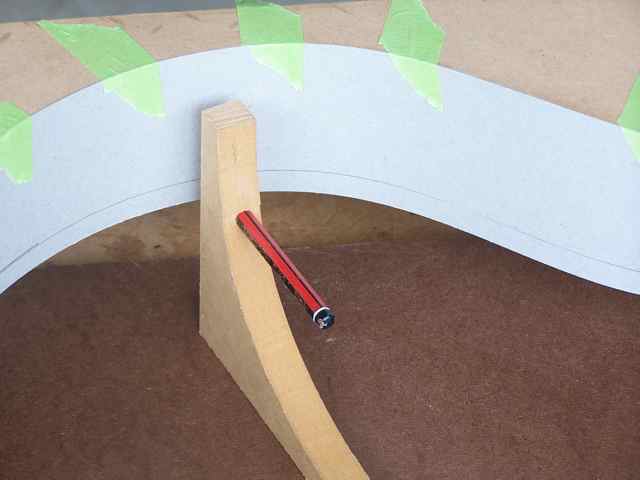
I just cut out the shape with a scalpel and then used the template to lay out the side profile.
The sides are run through the table saw to give a nice straight edge for the top, and side depth is registered from this edge. On this instrument its 3" deep at the butt, and 1" at the headstock joint. You need to take the top and back thickness into account when you do your layout. I also bend my sides registered off of the butt joint, so I've squared a line off a few mm in from the edge to give me a little wiggle room in case the side slips a little in the bender.
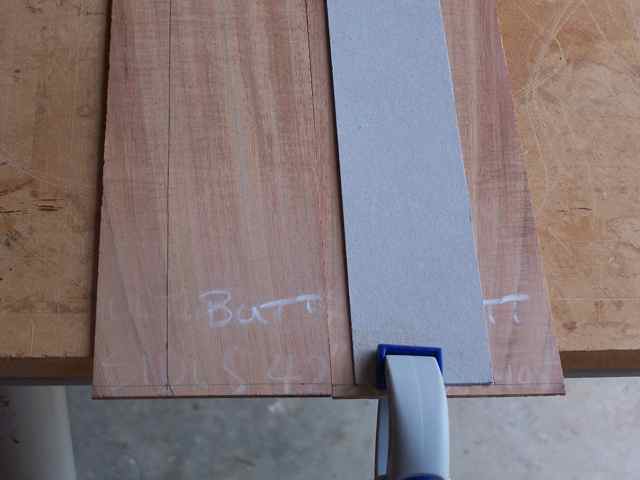
Mark off the depth at the butt, and at the head stock. Lay on the template and pencil in the line.
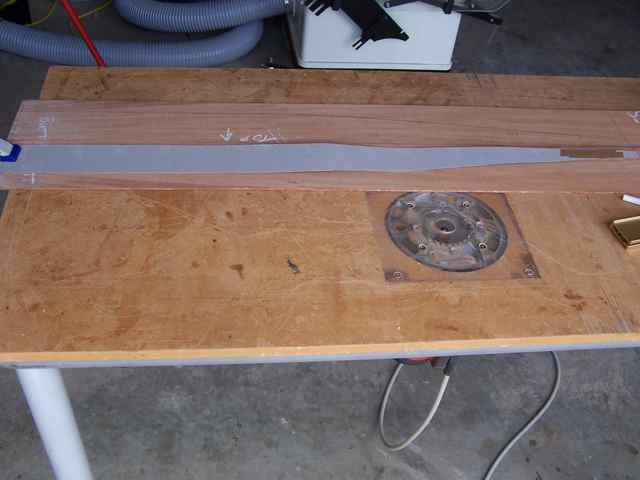
Cut the sides to the correct profile.
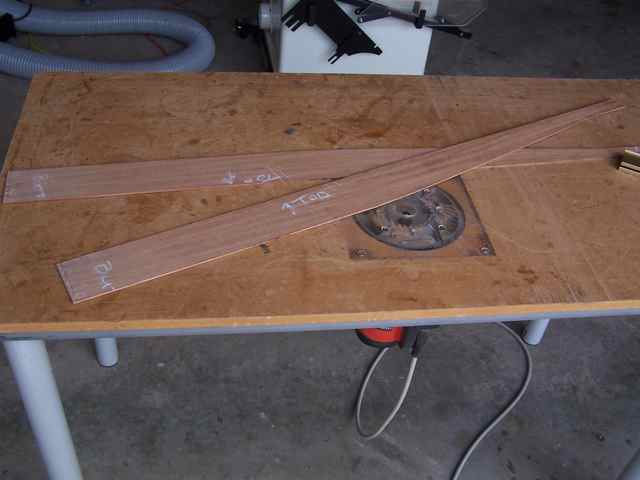
Load the first side into the side bender and proceed as usual.
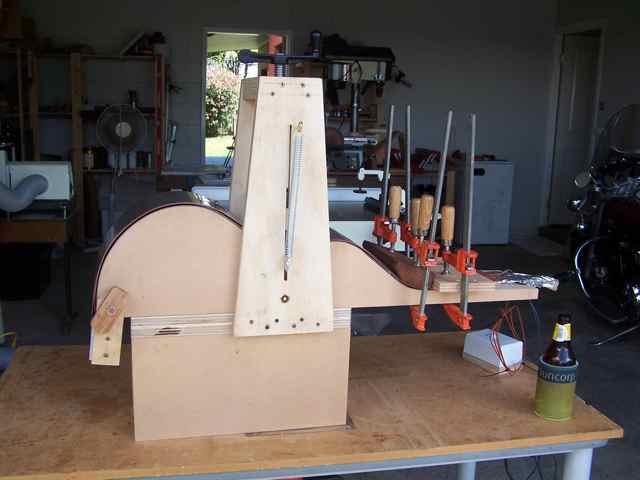
This was the first time to use my new side bender, and it works a treat. To bend Weissenborn sides I'm going to need to come up with a little easier way to bend the upper bout / neck area. Perhaps something along the lines of the press for a Venetian cutaway. This method worked, but it takes more hands than I have.
